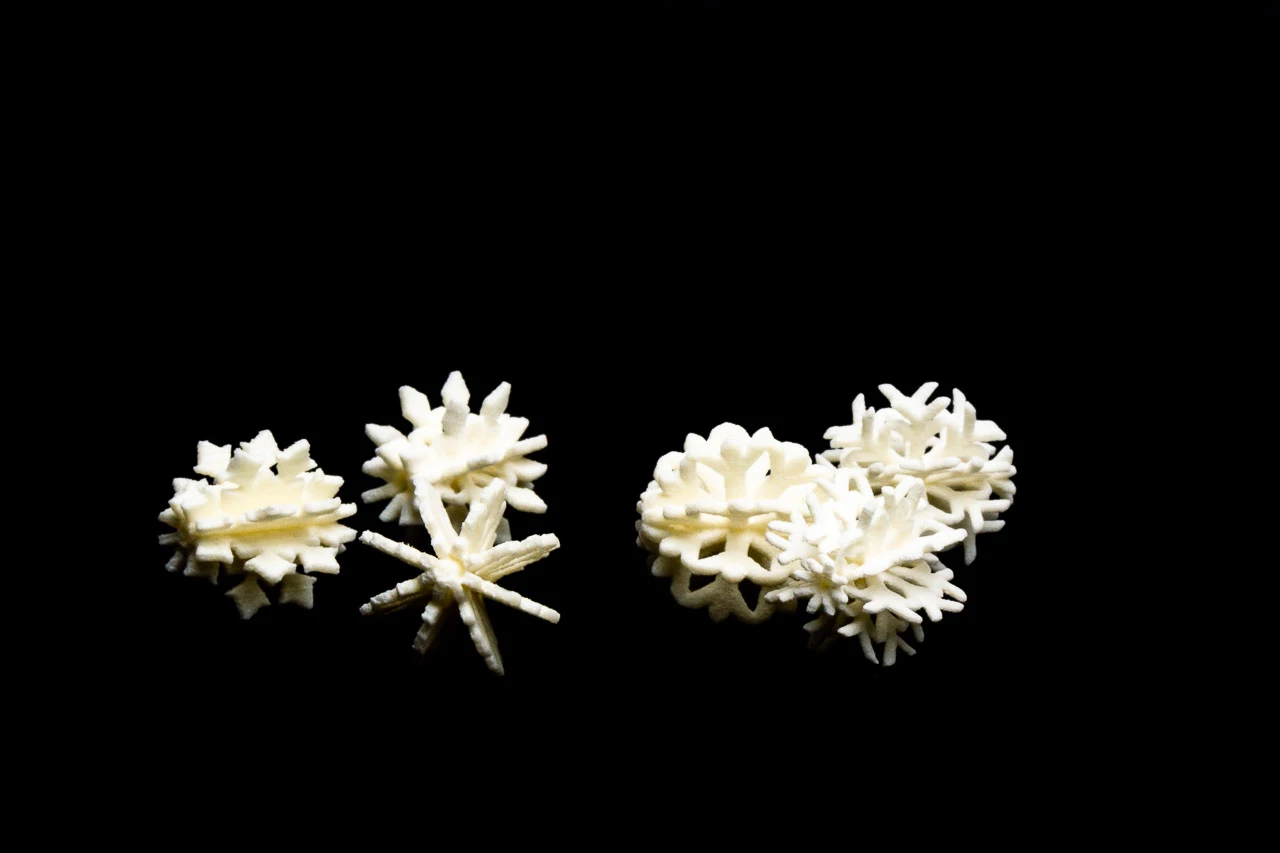
25.04.2022 von Dr. Elena Moukhina, Dr. Natalie Rudolph, Dr. Stefan Schmölzer
3D-Druck: Kristallisationskinetik von Polyamid 12 während des selektiven Lasersinterns
Powder Bed Fusion (PBF), auch als Selektives Lasersintern (SLS) bezeichnet, ist eine Technologie zum schichtweisen Aufbau von 3D-Objekten, bei der ein Laserstrahl selektiv über einen vordefinierten Bereich der Pulverschicht fährt. Eines der dabei am häufigsten verwendeten Materialien ist PA12.
Powder Bed Fusion (PBF), auch als Selektives Lasersintern (SLS) bezeichnet, ist eine Technologie zum schichtweisen Aufbau von 3D-Objekten, bei der ein Laserstrahl selektiv über einen vordefinierten Bereich der Pulverschicht fährt. Das Pulver wird an diesen Stellen durch den Laserstrahl aufgeschmolzen und könnte beim Auftragen der nächsten, kälteren Pulverschicht beginnen zu kristallisieren. Dieser Vorgang wird so lange wiederholt, bis das gesamte Teil fertiggestellt ist. Eine vollständige Beschreibung des Verfahrens ist in [2] zu finden.
Eines der dabei am häufigsten verwendeten Materialien ist PA12, jedoch schreitet die Entwicklung von Modifikationen oder weiteren Materialien mit verbesserten oder unterschiedlichen Eigenschaften stetig voran.
Bevor man mit einem neuen Material zu arbeiten beginnt, ist es sehr wichtig, dessen Kristallisationsverhalten zu kennen, um die für den SLS-Prozess optimalen Temperaturen zu finden. Diese Temperaturen zählen zu den wichtigsten Parametern des Sinterprozesses, der sowohl die Druckgeschwindigkeit als auch die Qualität des Endprodukts beeinflusst. Der herkömmliche empirische Ansatz nimmt sehr viel Zeit in Anspruch und gestaltet sich daher kostspielig. Im Gegensatz dazu kann die Qualifizierung eines neuen Materials mit der Software Kinetics Neo zur kinetischen Modellierung der Kristallisationsgeschwindigkeit auf Grundlage von DSC-Daten und anschließender Simulation des Prozesses für unterschiedliche Temperaturprofile viel schneller erfolgen.
Nach Durchführung der experimentellen DSC-Messungen können diese Daten einer kinetischen Analyse zur Erstellung des kinetischen Modells unterzogen werden. Dieses Modell wird dann zur Simulation verschiedener möglicher Temperaturszenarien des Prozesses zur Findung des optimalen Modells eingesetzt.
Experimenteller Teil
Mit der DSC-Messtechnik lassen sich Schmelz– und Kristallisationstemperaturen während der Aufheizung und Abkühlung bestimmen. Diese Temperaturen definieren das Prozessfenster für die SLS-Technologie [1]. Diese Temperaturen hängen jedoch von den Abkühl- und Aufheizraten ab, da beide Prozesse zeitabhängig sind. Für niedrigere Aufheiz- und Abkühlraten wird das Prozessfenster verkleinert, was weitere isotherme Messungen voraussetzt [2].
Mittels isothermer Messungen werden Informationen über die isotherme Kristallisationsrate bei unterschiedlichen Temperaturen erhalten. Diese Kristallisationsrate ist abhängig vom Unterkühlungsgrad eines Materials. Je niedriger die Temperatur, desto höher ist der Unterkühlungsgrad und umso höher die Kristallisationsrate. Diese Abhängigkeit ist bei den experimentellen Messungen für PA12, durchgeführt mit der DSC 214 Polyma (Abb.1), deutlich zu sehen. Diese Untersuchungen wurde an PA12-Proben mit einer Probeneinwaage von ca. 5 mg in Aluminiumtiegeln (Concavus® Al) mit geschlossenem Deckel unter Stickstoff durchgeführt. Das hier gezeigte Isothermsegment folgt auf eine schnelle Abkühlrampe von Temperaturen oberhalb der Schmelztemperaturen und SchmelzenthalpienDie Schmelzenthalpie einer Substanz, auch bekannt als latente Wärme, stellt ein Maß der Energiezufuhr dar, typischerweise Wärme, welche notwendig ist, um eine Substanz vom festen in den flüssigen Zustand zu überführen. Der Schmelzpunkt einer Substanz ist die Temperatur, bei der die Substanz von einem festen (kristallinen) in den flüssigen Zustand (isotrope Schmelze) übergeht.Schmelztemperatur.
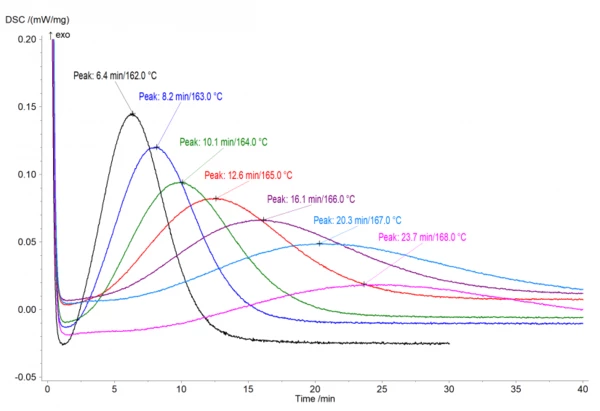
Kinetische Analyse
Die kinetische Analyse der DSC-Messungen für die isotherme KristallisationAls Kristallisation bezeichnet man den physikalischen Vorgang der Verhärtung bei der Bildung und beim Wachstum von Kristallen. Bei diesem Prozess wird Kristallisationswärme frei.Kristallisation bei unterschiedlichen Temperaturen wurde mit der NETZSCH Kinetics Neo-Software durchgeführt. Das Ergebnis ist ein zeit- und temperaturabhängiges Modell, mit dem alle experimentellen Kurven bei verschiedenen Temperaturen beschrieben werden können. Dieses Modell berechnet die Kristallisationsrate anhand folgender kinetischer Gleichung:
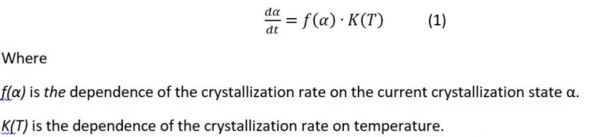
Bei der isothermen Analyse der Kristallisation wird die erste Abhängigkeit typischerweise durch die Avrami-Gleichung dargestellt, die die Keimbildungsgeschwindigkeit widergibt.

Die erweiterte Version der Avrami-Gleichung (4, Erläuterung am Ende des Artikels) ist die Sestak-Berggren-Gleichung (5, Erläuterung am Ende des Artikels). Diese erweiterte Gleichung wird in vorliegender Analyse verwendet, da sie eine bessere Anpassung an die experimentellen Daten ermöglicht.

Die Abhängigkeit K(T) in Gleichung (1) ist eine formale Arrhenius-Gleichung als abnehmende Abhängigkeit der Temperatur mit Präexponenten A und scheinbarer Aktivierungsenergie E:

Das kinetische Modell (Eq1) zeigt die Abhängigkeit der gegenwärtigen Kristallisationsgeschwindigkeit von der Temperatur und dem aktuellen Kristallisationsgrad.
Die Gleichungen enthalten unbekannte Parameter, die von der Software ermitteln werden konnten, um die beste Anpassung an die experimentellen Kurven zu finden.
Wird diese Simulation für die Temperaturbedingungen der isothermen Experimente mit optimalen Parametern durchgeführt, ergibt sich eine sehr gute Übereinstimmung zwischen Experiment und Simulation mit R2=0,998. In Abbildung 2 stellen die Punkte die experimentellen Daten und die durchgezogenen Linien die Simulation gemäß den Gleichungen (1,3,4) dar.
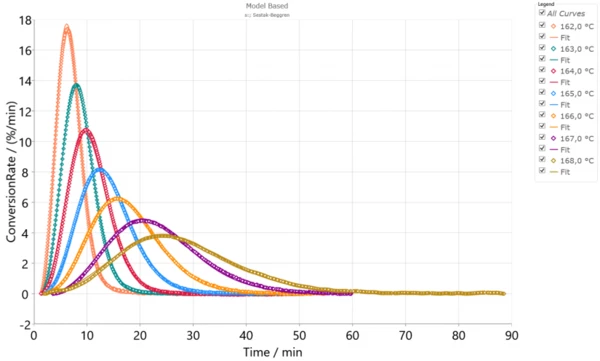
Simulationen
Dieses eine Modell lässt sich nun auf verschiedene Temperaturen anwenden und kann somit zur Simulation der Kristallisation im SLS-Prozess eingesetzt werden. Das Temperaturprofil der Pulveroberfläche kann über mehrere Zyklen hinweg bestimmt werden. Anschließend lässt sich eine Simulation des Kristallisationsprozesses durchführen. Es kann davon ausgegangen werden, dass jede niedrigere Schicht ein ähnliches Temperaturprofil aufweist, jedoch aufgrund des Pulverauftrags für jede Schicht mit leicht niedrigeren Temperaturen. Somit lässt sich der Kristallisationsprozess der einzelnen Schicht während mehrerer Laserzyklen simulieren. Abbildung 3 zeigt die Simulation des Kristallisationsgrades über 5 Zyklen, wobei für jeden neuen Zyklus bzw. jede neue Schicht die Temperatur um 2 K verringert wurde.
Es ist ersichtlich, dass eine Schicht für eine Zyklusdauer nicht vollständig kristallisiert werden kann, solange sie die oberste Schicht des Pulverbetts ist. Die Kristallisation dieser Schicht lässt sich jedoch fortsetzen, wenn diese die zweite von oben ist, dann die dritte von oben usw. Die Kristallisation über mehrere Zyklen legt den Vorteil des SLS-Verfahrens offen, wenn das entstehende 3D-Objekt eine sehr starke Schichthaftung und isotrope mechanische Eigenschaften hinsichtlich Härte, Zugfestigkeit und DehnungDehnung beschreibt die Deformation eines Materials, das durch eine von außen einwirkende Kraft oder Spannung mechanisch belastet wird. Gummimischungen zeigen Kriech-Eigenschaften, wenn eine statische Last aufgebracht wird.Dehnung aufweist [3].
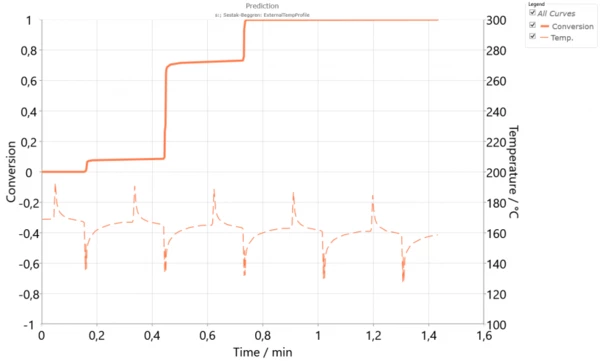
Erhöht man jedoch die Dicke, vergrößert sich der Temperaturunterschied zwischen den Schichten, was beim Hochgeschwindigkeitssintern der Fall sein kann. Die Simulation über 5 Zyklen mit einem Temperaturunterschied von 5 K (Abbildung 4) zeigt, dass die Hauptkristallisation bereits während des zweiten Zyklus‘ beendet ist, während die dritte Schicht bereits fest ist. Diese sehr asynchrone Kristallisation könnte der Grund für die mechanischen Spannungen und das Verziehen oder die Krümmung in der Probe sein, die während des SLS-Prozess vorkommen kann. Auch könnte durch Verwendung dickerer Pulverschichten die Isotropie des Bauteils verringert werden.
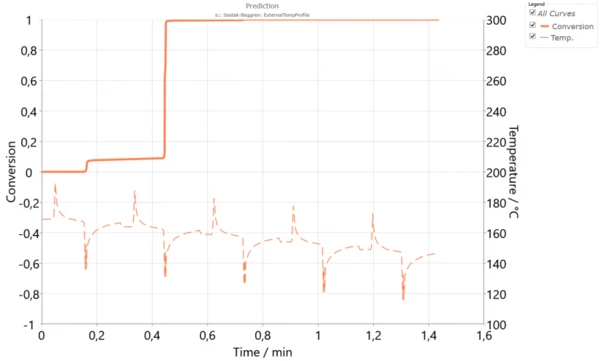
Zusammenfassung
In Kombination mit DSC-Geräten ist die NETZSCH Kinetics Neo Software für unsere Anwender bei der Untersuchung des Kristallisationsverhalten von Materialen (Polymeren) und der Simulation ihres Verhaltens für derart komplexe industrielle Prozesse wie dem 3D-Druck mittels selektiver Lasersintertechnologie äußert hilfreich. Dies ist besonders wichtig für das Finden optimaler Temperaturprogramme für neue Materialien, die beim SLS-Verfahren eingesetzt werden.
Lesen Sie auch / Quellen:
- https://ta-NETZSCH.com/how-to-determine-the-process-window-for-sls-powders-using-dsc
- https://ta-NETZSCH.com/how-to-study-the-isothermal-crystallization-behavior-of-sls-powder-using-dsc
- https://3dinsider.com/sls-printing/
- https://doi.org/10.1016/j.tca.2011.03.034
- https://doi.org/10.1016/0040-6031(71)85051-7
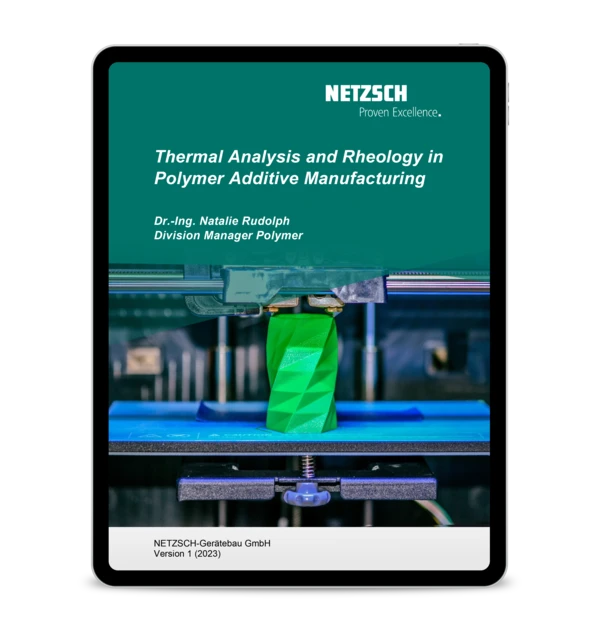
FREE E-Book
Thermal Analysis and Rheology in Polymer Additive Manufacturing
Discover the secrets behind AM's game-changing capabilities! Our newly released ebook delves deep into the heart of AM, unveiling the power of reliable material characterization techniques, specifically thermal analysis and rheology.